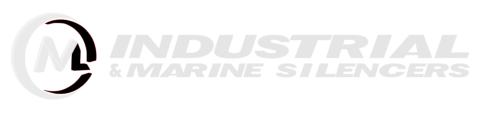
ML Industrial Exhaust Silencers is a company specialising in high quality Exhaust Gas Silencers fabrication, producing high quality acoustic solutions for the power generation industries.
More than 28 years experience in the manufacture our expertise ranges from basic pipework to complex metal fabrications. Key to our success is our knowledge of the very specialist metal welding and fabrication techniques which ensures or clients get the best solution to their engineering problems.
Our attention to detail at every stage in the project means clients have peace of mind in the quality of our work and reassurance that it will be delivered on time.


HISTORY
During the initial decade of the 19th century the first patent was applied for an exhaust gas silencer for a reciprocating engine powered by petroleum(gasoline) in America. The patent along with a second for a 0.22 bore long barrelled target rifle silencer was made by Hiram Percy Maxim, the son of Hiram Stevens Maxim who invented the Maxim Machine gun.
The rifle silencer unfortunately had a relatively short life, as it was deemed mistakenly, that it could be used on handheld weapons by criminals and political pressures, were taken to discourage its sale. However, its parallel patent for the exhaust gas silencer product became a great success and the company bearing the Maxim name still exists in the USA today after several owners have come and gone in the last 125 years.
During this period associations with several British manufacturers, were made and as the patent’s overall life lapsed, the original and modified designs are still being constructed in the United Kingdom and they can be purchased today for most of the Diesel-, Petrol- and Gas-powered prime movers currently on the market today. We, due to historical associations with original company still use some of the design techniques and philosophies developed over that time.
FUTURE
Sadly, the outlook for the two and four stroke reciprocating engines in all its varied forms along with gas turbine and associated jet powered derivatives due to the pressures of the current Global warming phenonium and the additional effects of the use of further addition use of fossil fuels, puts the whole industry in jeopardy in the next twenty years.
Although, great strides have been made by the use of catalytic, SCR systems, which effectively reduce the noxious emissions found in exhaust gas, no effective solution to the total reduction of carbon monoxide and carbon dioxide has been found to reduce the overall increase of the same levels of gases in our rather thin protective atmosphere and a total conversion to fully electric power may be the only solution, with all the addition implications that may result in that decision.
PRODUCT RANGE
The product range, which is constantly, under review, uses three fundamental types of designs. The first of these is the highly versatile Reactive Expansion/Reflection principle, which relies upon two or three chambers of varying sizes with specifically designed bypass tubes leading from one chamber to the next.
The exhaust gas expands within each chamber slowing it down, as well as the predominant firing frequency being reflected towards its initial source so diminishing its intensity. The exhaust gas velocity is then increased within the bypass tubes to repeat the process in a second or third chamber, The sizes of each chamber are calculated to give the possible insertion loss at the firing frequency of the prime mover and its sub-harmonics.
Dependent upon the silencer size total noise reduction can be between 18.0 dB(A) and 32.0 dB(A). It should be noted that the best performance is between 63.0 to 1,000.0 cycles per second, but the insertion loss reduces significantly at the higher centre frequencies of the spectrum.
The second type is the Dissipative or Absorption silencer, which comprises of a straight through perforated tube with an absorption layer on the external surface usually glass silk or high temperature mineral fibre.
The varied individual staple lengths of the fibre, vibrate at different frequencies as they are excited by the exhaust gas noise, the vibrations create heat and a simple energy conversion from noise energy to heat energy is carried out. This again reduces the noise intensity to a lower level.
The dissipative range of exhaust gas silencer is more effective at the higher centre frequencies from 500 hertz to 4,000.0 hertz. In some applications to increase the performance a central pod or annular splitter may be used.
The depth of the absorption layer is critical to get the best performance. Insertion losses can range from 15.0 dB(A) to 45.0 dB(A) in ideal conditions. The third type is the Combination silencer which uses the attributes of both previously described variants to obtain a good overall insertion loss in a restricted space.
Again, the overall reductions can vary from 15.0 dB(A) to 45.0 dB(A) dependent upon the equipment used. In real terms it is extremely difficult to exceed an insertion loss of 50.0 dB(A) with a single silencer type. It should also be noted that all internal combustion engines, have a maximum back pressure limit, that can be imposed by the exhaust gas system.
This is stipulated by the engine manufacturer as it affects both power output and fuel consumption. We pride ourselves on being able to precisely determine the total back pressure of a single silencer to a complete exhaust gas system.


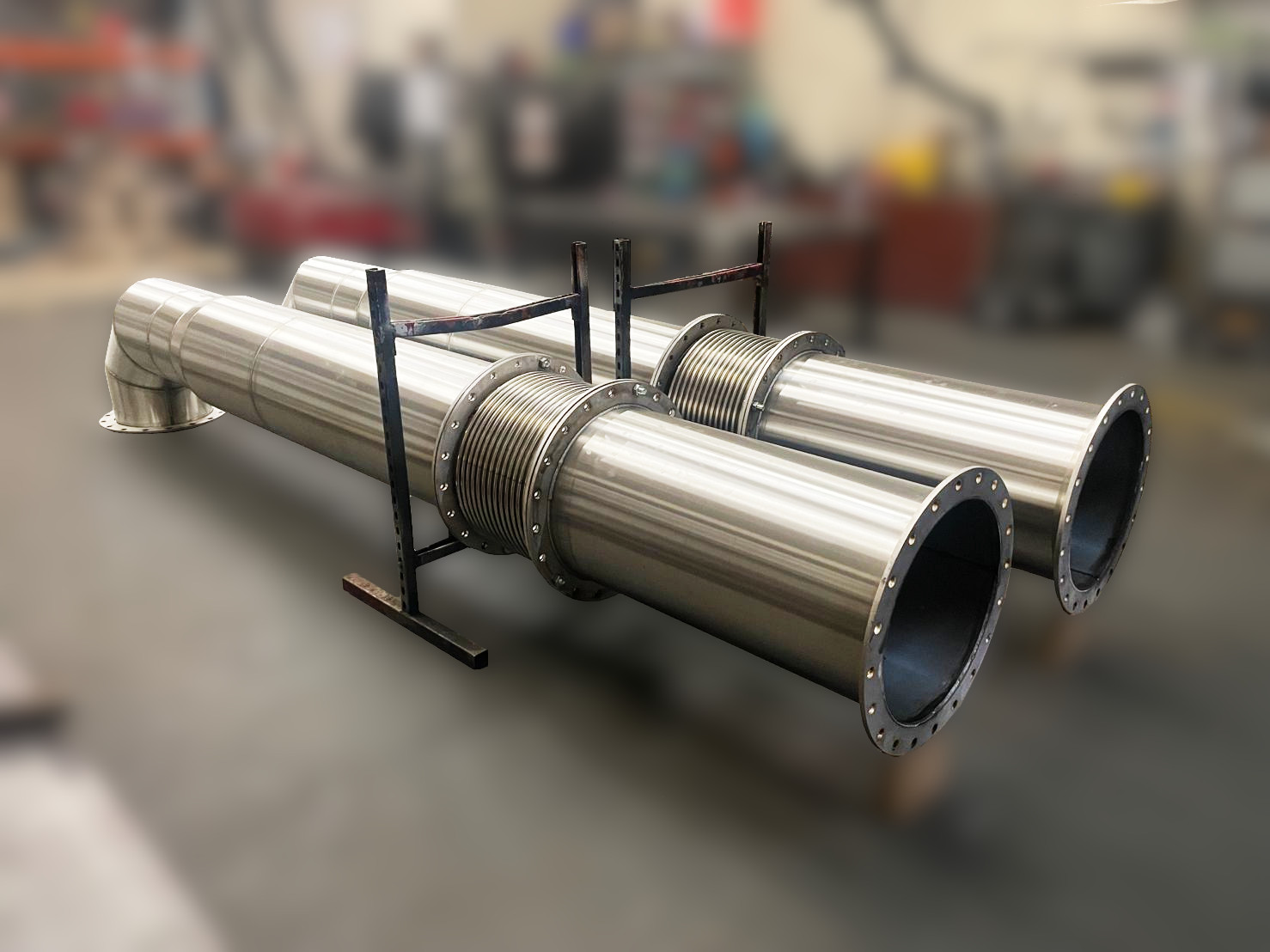


MANUFACTURE, MATERIAL & FINISH
All our equipment regardless of its size or complicated design, is manufactured in our own modern premises, with exceptionally skilled operatives, who have the highest national qualifications in fabrication, welding and ‘On Site’ installations and copies of the same a readily available for any prospective client.
We will also provide any detailed Health and Safety documentation and Method Statements or each application we are dealing with. The company can provide exhaust gas silencers and pipework installations in Mild Steel, Stainless Steel, Corten A and B and other more exotic materials as requested.
Apart from the standard high temperature painted finishes, we can also provide, Shot blast, aluminium, or Zinc metal spray protection with an outer high temperature silicone sealer to the current British standards.
We can also provide specific designs for hot dip galvanising or similar at additional cost. There are no areas which we cannot cover and we are eminently capable of producing high pressure equipment to British standard requirement.
COMPLETE EXHAUST GAS SYSTEMS AND INSTALLATIONS
Most companies offer lists of the varying exhaust silencers that they manufacture, with dimensions. However, we have taken a different route, as the types of exhaust gas mufflers is now so varied and installation requirements are so varied.
We prefer, to treat enquiry application upon its own merits and not be restricted in size, type or defined parameters. This allows us to be proactive and supply not only the exhaust gas silencer, but complete exhaust gas systems, installation, and protection from heated services in each individual case.
We will also supply all associated steel support structures and any ancillary items if required. We have supplied numerous installations with specifically designed Box type exhaust gas silences with integrated support structures and outlet pipework to the termination point.
The company also offers a service to extend or replace existing exhaust gas systems, with on-site manufacture in places where access is restricted or due to height standard means of lifting are prohibitive.